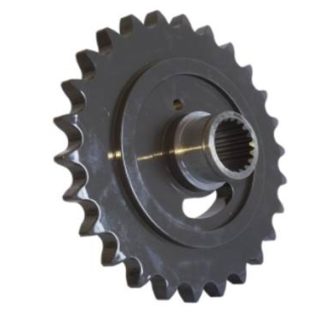
Расчет звездочки цепной передачи по шагу цепи
Изделия с зубчатой передачей находят даже в раскопках древнегреческих и древнеримских городов. Леонардо да Винчи не только написал «Мону Лизу», но и первым описал механизм передачи механической энергии на значительные расстояния при помощи двух валов (звездочек в современной интерпретации) и цепи. Но его изобретение еще долго оставалось невостребованным. Только на рубеже 18-го и 19-го начался этап бурного развития промышленности. И именно тогда зубчатой передаче нашли достойное применение.
За два столетия ее механизм существенно усовершенствовали. Для цепей разработали стандарты, регламентирующие шаг, диаметр и прочие параметры. Но проблема правильного построения звездочек остается неизменно актуальной.
Это связано с тем, что при проектировании валов необходимо одновременно учитывать несколько требований:
- вращательный момент с минимальной задержкой должен передаваться от ведущей звездочки на ведомую;
- движение цепи должно быть непрерывным и плавным;
- вся цепная передача в процессе работы должна оставаться в заданной плоскости.
Чтобы выполнить все перечисленные условия, звездочки следует подбирать строго в соответствии с предварительно проведенными расчетами.
Базовые параметры звездочек
В России производители звездочек обязаны работать по ГОСТ 591-69. В соответствии с ним для начала проектирования звездочки нужны следующие данные:
- Шаг цепи (t).
- Необходимое число зубцов на звездочке (z).
- Диаметр окружности зацепления (d1).
Геометрическая форма готового изделия зависит от следующих параметров:
- Диаметр делительной окружности (D дел).
- Диаметр окружности выступов (D выст).
- Радиус впадин (r).
Построение звездочки: как рассчитать необходимые параметры?
Чтобы получить звездочку, идеально соответствующую всем предъявляемым требованиям, расчеты проводят в соответствии с формулами, приведенными ниже:
- Оси шарниров цепных звеньев в процессе работы прилегают к делительной окружности. Чтобы рассчитать ее диаметр, потребуется формула:
- Следующий шаг предполагает определение окружности выступов по формуле:
- Определить радиус впадин позволяет формула:
- Рассчитать диаметр окружности впадин можно по формуле:
Для D выст допустимая погрешность не превышает 0,1 мм. Для всех иных параметров отклонение не может превышать 0,01 мм.
Конструктивные особенности ступицы и диска применительно к звездочкам цепных передач
Чтобы избежать деформаций диска, его неравномерного крепления и последующего биения в процессе вращения, его в большинстве случаев отливают вместе со ступицей. Как вариант, изготовление ведется на фрезерном станке.
Задача ступицы в данном случае — крепление диска к передающему или принимающему узлу оборудования с цепной передачей. Если в процессе изготовления и сборки вала соблюдены требования ГОСТ, при вращении диска не будет ни осевых, ни радиальных биений.
На практике при построении звездочки применяют следующие способы крепления вала:
- на шлицу. Этот актуально для цепных приводов, работающих на повышенных скоростях и/или под значительными нагрузками;
- на шпонки. Этот вариант используют, если скорость вращения вала невелика.
Диаметр ступицы подбирают так, чтобы она позволяла решать поставленную задачу, но сама не создавала избыточную нагрузку на механизм.
Если ступица требуется для узла из чугуна, ее диаметр стандартно равен диаметру вала * 1,65. Если же узел стальной, диаметр вала умножают на 1,55.
Другой важный параметр — длина ступицы. Стандартно для ее расчета диаметр вала умножают на числа из диапазона 1,2–1,5.
Из какого материала производят звездочки для цепных передач?
Механическая нагрузка — не единственный негативный фактор, влияющий на работоспособность цепей и звездочек. Есть еще кислоты, щелочи, конденсат и т. д. Это приводит к тому, что все узлы цепной передачи надлежит изготавливать из материалов, устойчивых к коррозии, нагрузкам: ударным, на разрыв и т. д.
Предпочтение отдают среднеуглеродистым сталям. Если изделие должно соответствовать особым требованиям, работать в особо сложных условиях, в состав вводят особые легирующие добавки. Уже готовую звездочку (отлитую или выточенную) дополнительно:
- пропускают через термическую обработку. Требуемая твердость — 45–55 ед.;
- либо подвергают цементированию. Глубина слоя составляет 1–1,5 мм. И только после этого помещают в печь ТВЧ. Твердость в этом случае должна составлять 55–60 ед.
Для особых случаев используют цепи и звездочки не стальные, а из особых композитных материалов: текстолита, полиамидов, полиформальдегидов. В этом случае вся система работает с минимальным шумом и вибрацией. Звенья цепей практически не ударяются о зубья цепи. Но их используют в малоответственных транспортных системах, не находящихся постоянно под нагрузкой.
Чугун — еще один материал для построения и изготовления звездочек цепной передачи. Но сфера его применения ограничена. Такие изделия не предназначены для работы на больших скоростях. Разрешенный максимум — 2 м/с. Ограничения затрагивают и динамические нагрузки. Они должны быть минимальными.
Для повышения твердости чугунные цепные передачи проводят через закалку. Рекомендованное значение на выходе — 330–430 ед. по HB.
Цепи из чугуна часто устанавливают на тракторах, комбайнах, дорожной и строительной спецтехнике. В этом случае выбирают упрочненные чугуны, что позволяет снизить коэффициент трения. Если же вся система должна работать в условиях повышенных динамических нагрузок, звенья цепи и собственно звездочки покрывают тонким слоем тефлона.